Krydsfiner er lavet af tre eller flere tynde lag træ, der er limet sammen med et klæbemiddel. Hvert lag træ, eller krydsfiner, er normalt orienteret med åretegningerne vinkelret på det tilstødende lag for at reducere krympningen og forbedre det færdige stykkes styrke. Det meste krydsfiner presses til store, flade plader, der bruges i byggeri. Andre krydsfinerstykker kan formes til simple eller sammensatte kurver til brug i møbler, både og fly.
Brugen af tynde lag træ som konstruktionsmiddel dateres tilbage til omkring 1500 f.Kr., da egyptiske håndværkere limede tynde stykker mørkt ibenholt på ydersiden af en cedertræskiste fundet i Kong Tut-Ankh-Amons grav. Denne teknik blev senere brugt af grækerne og romerne til at producere fine møbler og andre dekorative genstande. I 1600-tallet blev kunsten at dekorere møbler med tynde træstykker kendt som finering, og selve stykkerne blev kendt som finér.
Indtil slutningen af 1700-tallet blev finerstykkerne skåret udelukkende i hånden. I 1797 ansøgte englænderen Sir Samuel Bentham om patenter, der dækkede adskillige maskiner til fremstilling af finer. I sine patentansøgninger beskrev han konceptet med at laminere flere lag finer med lim for at danne et tykkere stykke – den første beskrivelse af det, vi nu kalder krydsfiner.
Trods denne udvikling tog det næsten yderligere hundrede år, før laminerede finer fandt kommerciel anvendelse uden for møbelindustrien. Omkring 1890 blev lamineret træ for første gang brugt til at bygge døre. Efterhånden som efterspørgslen voksede, begyndte flere virksomheder at producere plader af flerlags lamineret træ, ikke kun til døre, men også til brug i jernbanevogne, busser og fly. Trods denne øgede anvendelse skabte konceptet med at bruge "klistret træ", som nogle håndværkere sarkastisk kaldte det, et negativt image for produktet. For at imødegå dette image mødtes producenterne af lamineret træ og besluttede sig endelig for udtrykket "krydsfiner" til at beskrive det nye materiale.
I 1928 blev de første krydsfinerplader i standardstørrelse på 1,2 m x 2,4 m (4 ft x 8 ft) introduceret i USA til brug som et generelt byggemateriale. I de følgende årtier gjorde forbedrede klæbemidler og nye produktionsmetoder det muligt at bruge krydsfiner til en bred vifte af anvendelser. I dag har krydsfiner erstattet savet tømmer til mange byggeformål, og fremstilling af krydsfiner er blevet en milliardindustri på verdensplan.
De ydre lag af krydsfiner er kendt som henholdsvis forsiden og bagsiden. Forsiden er den overflade, der skal bruges eller ses, mens bagsiden forbliver ubrugt eller skjult. Midterlaget er kendt som kernen. I krydsfiner med fem eller flere lag er de mellemliggende lag kendt som tværbånd.
Krydsfiner kan være lavet af hårdttræ, nåletræ eller en kombination af de to. Nogle almindelige hårdttræstyper omfatter ask, ahorn, mahogni, eg og teak. Det mest almindelige nåletræ, der bruges til at lave krydsfiner i USA, er Douglasgran, selvom flere sorter af fyr, cedertræ, gran og redwood også bruges.
Kompositkrydsfiner har en kerne lavet af spånplade eller massive tømmerstykker, der er samlet kant mod kant. Den er færdigbehandlet med en krydsfinerfiner på for- og bagside. Kompositkrydsfiner bruges, hvor der er behov for meget tykke plader.
Den type klæbemiddel, der bruges til at binde trælagene sammen, afhænger af den specifikke anvendelse af den færdige krydsfiner. Nåletræskrydsfinerplader designet til montering på ydersiden af en struktur bruger normalt en phenol-formaldehydharpiks som klæbemiddel på grund af dens fremragende styrke og modstandsdygtighed over for fugt. Nåletræskrydsfinerplader designet til montering på indersiden af en struktur kan bruge et blodprotein- eller et sojabønneproteinklæbemiddel, selvom de fleste indvendige nåletræsplader nu er lavet med den samme phenol-formaldehydharpiks, der bruges til udvendige plader. Hårdttræskrydsfiner, der bruges til indvendige anvendelser og i møbelkonstruktioner, er normalt lavet med en urinstof-formaldehydharpiks.
Nogle anvendelser kræver krydsfinerplader med et tyndt lag plastik, metal eller harpiksimprægneret papir eller stof bundet til enten forsiden eller bagsiden (eller begge) for at give den ydre overflade yderligere modstandsdygtighed over for fugt og slid eller for at forbedre dens malingholdende egenskaber. Sådan krydsfiner kaldes overlagt krydsfiner og bruges almindeligvis i bygge-, transport- og landbrugsindustrien.
Andre krydsfinerplader kan belægges med en flydende bejdse for at give overfladerne et færdigt udseende, eller de kan behandles med forskellige kemikalier for at forbedre krydsfinerens flammemodstand eller modstandsdygtighed over for råd.
Der er to brede klasser af krydsfiner, hver med sit eget klassificeringssystem.
En klasse er kendt som bygge- og industriel. Krydsfiner i denne klasse bruges primært for deres styrke og vurderes efter deres eksponeringsevne og den type finer, der anvendes på forsiden og bagsiden. Eksponeringsevnen kan være indvendig eller udvendig, afhængigt af limtypen. Finerkvaliteter kan være N, A, B, C eller D. N-kvalitet har meget få overfladefejl, mens D-kvalitet kan have adskillige knaster og revner. For eksempel er krydsfiner, der bruges til undergulv i et hus, vurderet som "Indvendig CD". Det betyder, at det har en C-forside med en D-bagside, og limen er egnet til brug på beskyttede steder. De indre lag i al bygge- og industriel krydsfiner er lavet af finer i kvalitet C eller D, uanset klassificeringen.
Den anden klasse af krydsfiner er kendt som hårdttræ og dekorativ. Krydsfiner i denne klasse bruges primært for deres udseende og er klassificeret i faldende rækkefølge efter fugtbestandighed som Teknisk (Udvendig), Type I (Udvendig), Type II (Indvendig) og Type III (Indvendig). Deres overfladebeklædning er stort set fri for defekter.
Størrelser
Krydsfinerplader varierer i tykkelse fra 1,6 mm til 76 mm. De mest almindelige tykkelser ligger i området fra 6,4 mm til 19,0 mm. Selvom kernen, tværbåndene samt forsiden og bagsiden af en krydsfinerplade kan være lavet af finer af forskellig tykkelse, skal tykkelsen af hver plade være afbalanceret omkring midten. For eksempel skal forsiden og bagsiden være af samme tykkelse. Ligeledes skal de øverste og nederste tværbånd være lige store.
Den mest almindelige størrelse på krydsfinerplader, der anvendes i byggeri, er 1,2 m i bredden og 2,4 m i længden. Andre almindelige bredder er 0,9 m og 1,5 m. Længderne varierer fra 2,4 m til 3,6 m i intervaller af 0,3 m. Særlige anvendelser, som f.eks. bådbygning, kan kræve større plader.
Træerne, der bruges til at lave krydsfiner, har generelt mindre diameter end dem, der bruges til at lave tømmer. I de fleste tilfælde er de blevet plantet og dyrket i områder, der ejes af krydsfinerfirmaet. Disse områder forvaltes omhyggeligt for at maksimere træernes vækst og minimere skader fra insekter eller brande.
Her er en typisk rækkefølge af operationer til forarbejdning af træer til standard krydsfinerplader på 1,2 m x 2,4 m (4 ft x 8 ft):
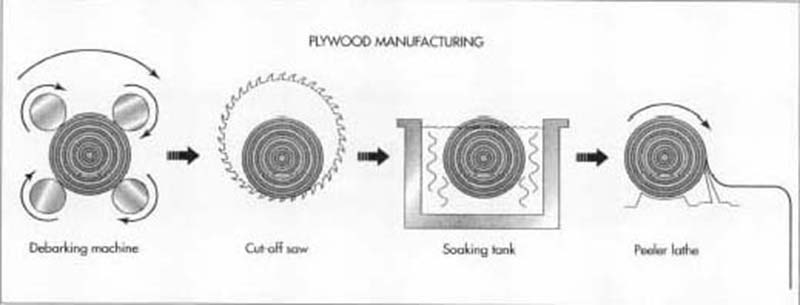
Træstammerne afbarkes først og skæres derefter i skrælleblokke. For at skære blokkene i finerstrimler, lægges de først i blød og skrælles derefter i strimler.
1 Udvalgte træer i et område markeres som klar til at blive fældet. Fældningen kan udføres med benzindrevne motorsave eller med store hydrauliske sakse monteret på forsiden af hjulkøretøjer kaldet fældere. Grenene fjernes fra de væltede træer med motorsave.
2 De beskårne træstammer, eller træstammer, slæbes til et læsseområde af hjulkøretøjer kaldet skidders. Træstammerne skæres til i længder og læsses på lastbiler til turen til krydsfinermøllen, hvor de stables i lange bunker kendt som træstammedæk.
3 Efterhånden som der er brug for træstammer, samles de op fra trædækkene af gummihjulslæssere og placeres på en kædetransportør, der bringer dem til afbarkningsmaskinen. Denne maskine fjerner barken, enten med skarptandede slibeskiver eller med højtryksvandstråler, mens træstammen langsomt roteres om sin længdeakse.
4 De afbarkede træstammer føres ind i møllen på en kædetransportør, hvor en enorm rundsav skærer dem i sektioner på ca. 2,5 m til 2,6 m, der er egnede til fremstilling af standardplader på 2,4 m. Disse træstammesektioner er kendt som skrælleblokke.
5 Før fineren kan skæres, skal skrælleblokkene opvarmes og lægges i blød for at blødgøre træet. Blokkene kan dampes eller nedsænkes i varmt vand. Denne proces tager 12-40 timer afhængigt af træsorten, blokkens diameter og andre faktorer.
6 De opvarmede skrælleblokke transporteres derefter til skrælledrejebænken, hvor de automatisk justeres og føres ind i drejebænken én ad gangen. Mens drejebænken roterer blokken hurtigt om sin længdeakse, skræller et knivblad i fuld længde et kontinuerligt ark finer fra overfladen af den roterende blok med en hastighed på 90-240 m/min. Når blokkens diameter reduceres til ca. 230-305 mm, skubbes det resterende stykke træ, kendt som skrællekernen, ud af drejebænken, og en ny skrælleblok føres på plads.
7 Det lange finerark, der kommer ud fra / drejebænken, kan bearbejdes med det samme, eller det kan opbevares i lange bakker i flere niveauer eller vikles på ruller. Under alle omstændigheder involverer den næste proces at skære fineren i brugbare bredder, normalt omkring 1,4 m (4 ft-6 in), til fremstilling af standard krydsfinerplader med en bredde på 1,2 m (4 ft). Samtidig leder optiske scannere efter sektioner med uacceptable defekter, og disse klippes ud, hvilket efterlader finerstykker med mindre bredde end standard.
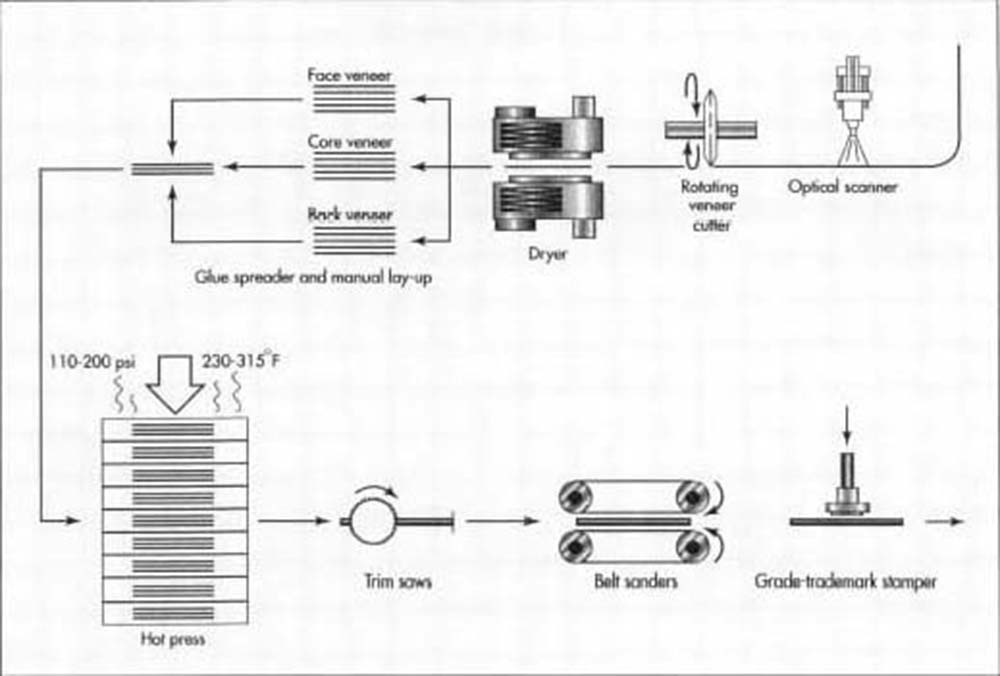
De våde finerstrimler vikles til en rulle, mens en optisk scanner registrerer eventuelle uacceptable defekter i træet. Når fineren er tør, sorteres og stables den. Udvalgte sektioner af finer limes sammen. En varmpresse bruges til at forsegle fineren til ét massivt stykke krydsfiner, som vil blive trimmet og slebet, før den præges med den passende kvalitet.
8 Finersektionerne sorteres og stables derefter efter kvalitet. Dette kan gøres manuelt, eller det kan gøres automatisk ved hjælp af optiske scannere.
9 De sorterede sektioner føres ind i en tørretumbler for at reducere deres fugtindhold og give dem mulighed for at krympe, før de limes sammen. De fleste krydsfinerfabrikker bruger en mekanisk tørretumbler, hvor stykkerne bevæger sig kontinuerligt gennem et opvarmet kammer. I nogle tørretumblere blæses stråler af højhastigheds, opvarmet luft hen over overfladen af stykkerne for at fremskynde tørreprocessen.
10 Når finerstykkerne kommer ud af tørretumbleren, stables de efter kvalitet. Undersidestykkerne har ekstra finer, der er splejset på med tape eller lim for at gøre stykkerne egnede til brug i de indvendige lag, hvor udseende og styrke er mindre vigtigt.
11 De sektioner af finer, der skal installeres på tværs – kernen i trelagsplader eller tværbåndene i femlagsplader – skæres i længder på ca. 1,3 m.
12 Når de passende sektioner af finer er samlet til en bestemt række krydsfiner, begynder processen med at lægge og lime stykkerne sammen. Dette kan gøres manuelt eller halvautomatisk med maskiner. I det enkleste tilfælde af trelagsplader lægges bagsidefineren fladt og køres gennem en limfordeler, som påfører et lag lim på den øvre overflade. De korte sektioner af kernefiner lægges derefter på tværs oven på den limede bagside, og hele pladen køres gennem limfordeleren en gang til. Til sidst lægges forsidefineren oven på den limede kerne, og pladen stables med andre plader, der venter på at komme i pressen.
13 De limede ark lægges i en varmpresse med flere åbninger. Presserne kan håndtere 20-40 ark ad gangen, hvor hvert ark lægges i en separat rille. Når alle arkene er fyldt, klemmer pressen dem sammen under et tryk på ca. 7,6-13,8 bar (110-200 psi), samtidig med at de opvarmes til en temperatur på ca. 109,9-157,2 °C (230-315 °F). Trykket sikrer god kontakt mellem finerlagene, og varmen får limen til at hærde ordentligt for maksimal styrke. Efter 2-7 minutter åbnes pressen, og arkene tages ud.
14 De ru plader passerer derefter gennem et sæt save, som skærer dem til deres endelige bredde og længde. Plader af højere kvalitet passerer gennem et sæt 1,2 m brede båndslibere, som sliber både forsiden og bagsiden. Plader af mellemkvalitet slibes manuelt for at rense ujævne områder. Nogle plader køres gennem et sæt rundsavklinger, som skærer lavvandede riller i forsiden for at give krydsfineren et struktureret udseende. Efter en sidste inspektion repareres eventuelle resterende defekter.
15 De færdige ark stemples med et kvalitetsmærke, der giver køberen information om eksponeringsklassificering, kvalitet, værksnummer og andre faktorer. Ark af samme kvalitetsmærke spændes sammen i stakke og flyttes til lageret for at afvente forsendelse.
Ligesom med tømmer findes der ikke noget perfekt stykke krydsfiner. Alle stykker krydsfiner har et vist antal defekter. Antallet og placeringen af disse defekter bestemmer krydsfinerkvaliteten. Standarder for bygge- og industrikrydsfiner er defineret af Product Standard PS1 udarbejdet af National Bureau of Standards og American Plywood Association. Standarder for hårdttræs- og dekorativ krydsfiner er defineret af ANSIIHPMA HP udarbejdet af American National Standards Institute og Hardwood Plywood Manufacturers' Association. Disse standarder etablerer ikke kun klassificeringssystemerne for krydsfiner, men specificerer også konstruktions-, ydeevne- og anvendelseskriterier.
Selvom krydsfiner udnytter træer ret effektivt – i bund og grund adskiller dem og samler dem igen i en stærkere og mere brugbar konfiguration – er der stadig betydeligt spild i fremstillingsprocessen. I de fleste tilfælde omdannes kun omkring 50-75 % af den brugbare mængde træ i et træ til krydsfiner. For at forbedre dette tal er flere nye produkter under udvikling.
Et nyt produkt kaldes orienteret spånplade, som fremstilles ved at rive hele træstammen i strenge i stedet for at skrælle en finer af træstammen og kassere kernen. Strengene blandes med et klæbemiddel og komprimeres til lag med træets årer i én retning. Disse komprimerede lag orienteres derefter vinkelret på hinanden, ligesom krydsfiner, og limes sammen. Orienteret spånplade er lige så stærk som krydsfiner og koster lidt mindre.
Opslagstidspunkt: 10. august 2021